Issue 48
Suscríbete
Featured Interview in K 2013: Reifenhäuser GmbH & Co. KG Maschinenfabrik
Troisdorf, 02.07.2013. Reifenhäuser Reicofil, the worldwide leading provider of spinbonding lines, is developing a new fibre-reinforced plastic and the corresponding process to manufacture it. The new semi-finished product is the first lightweight material on the market to combine reinforced fibre and nonwovens. In tests at the RWTH Aachen, where the new semi-finished product was directly compared to the current market standards in automotive engineering and aircraft construction, the new material came out on top in manufacturing process as well as for product properties.
Organic sheets are lightweight fibre composite parts with a thermoplastic matrix. The plate-shaped fibre composite material made of fibre tissue or fibre layers is embedded in a thermoplastic matrix, which is typically a plastic film. The individual layers of film and reinforced fibre are consolidated with heat and pressure and then cooled down to organic sheets. The plates can be reformed to component parts by reheating them.
Reifenhäuser Reicofil is the first to use nonwovens instead of film for the thermoplastic matrix. The development of this new semi-finished product means that an entire production step can be dispensed with during manufacturing. The new material additionally provides answers to some of the questions about organic sheets that have to date remained unsolved.
The production of the thermoplastic matrix (nonwovens) and its layering with reinforced fibre is done inline in one production step when manufacturing the new semi-finished product. In contrast to organic sheets, here the layers are not consolidated directly but rather wound onto reels. The layers adhere to one another but remain flexible. Both the consolidation of the layers and forming them into lightweight component parts then occurs once again in one single step. By combining individual production steps, less heating and cooling is required. The developers are anticipating positive effects to the energy efficiency of the entire process. The new semi-finished product can also be produced in large widths up to approx. 3 m and without limit to its length. Organic sheets are limited to widths of approx. 1.3 m.
The use of nonwovens has benefits not only in manufacturing but also for the product properties: Precisely during consolidation, the pressing together of individual layers, nonwovens have clear advantages over films. Tests have shown that the melt is distributed more uniformly between the reinforced-fibre. When being pressed together, no flaws arise anymore, because air can escape through the nonwovens. When pressing film together, air is frequently trapped, reducing the strength of the finished component part.
During subsequent processing of the finished component part, organic nonwovens have clear advantages due to their better drapability. In tests it was shown that extreme angles and details could be formed. Up to now forming has been tested only on smaller component parts up to a size of 200 mm x 200 mm. The developers anticipate these results will be transferable to larger parts. For more in-depth testing and further development of this technology to make it market-ready, the developers at
Reifenhäuser Reicofil are currently looking for partners in the industry. Together, it is planned to investigate which new lightweight construction markets can be opened by the new semi-finished product and the new manufacturing process.
The new composite fibre material and the new manufacturing process will be presented to the public for the first time at the K 2013, which runs from the 16th to the 23rd of October in Düsseldorf.
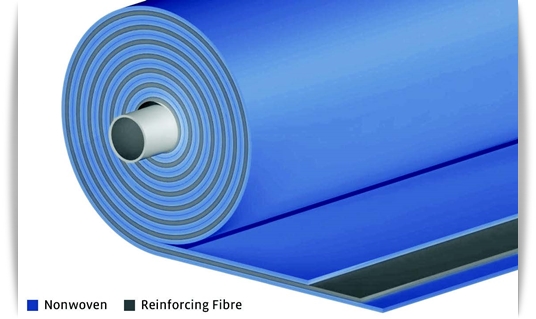
New rollable fibre-reinforced plastic combined with nonwovens
Internet: www.reicofil.com
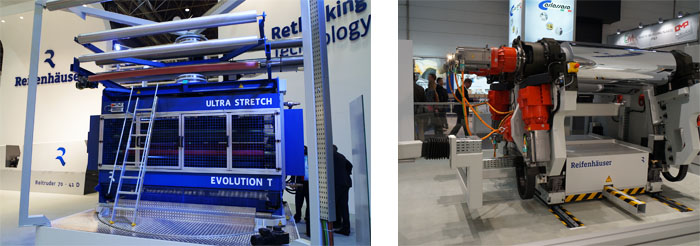
pic:Brilliant Show at K 2013
Organic sheets are lightweight fibre composite parts with a thermoplastic matrix. The plate-shaped fibre composite material made of fibre tissue or fibre layers is embedded in a thermoplastic matrix, which is typically a plastic film. The individual layers of film and reinforced fibre are consolidated with heat and pressure and then cooled down to organic sheets. The plates can be reformed to component parts by reheating them.
Reifenhäuser Reicofil is the first to use nonwovens instead of film for the thermoplastic matrix. The development of this new semi-finished product means that an entire production step can be dispensed with during manufacturing. The new material additionally provides answers to some of the questions about organic sheets that have to date remained unsolved.
The production of the thermoplastic matrix (nonwovens) and its layering with reinforced fibre is done inline in one production step when manufacturing the new semi-finished product. In contrast to organic sheets, here the layers are not consolidated directly but rather wound onto reels. The layers adhere to one another but remain flexible. Both the consolidation of the layers and forming them into lightweight component parts then occurs once again in one single step. By combining individual production steps, less heating and cooling is required. The developers are anticipating positive effects to the energy efficiency of the entire process. The new semi-finished product can also be produced in large widths up to approx. 3 m and without limit to its length. Organic sheets are limited to widths of approx. 1.3 m.
The use of nonwovens has benefits not only in manufacturing but also for the product properties: Precisely during consolidation, the pressing together of individual layers, nonwovens have clear advantages over films. Tests have shown that the melt is distributed more uniformly between the reinforced-fibre. When being pressed together, no flaws arise anymore, because air can escape through the nonwovens. When pressing film together, air is frequently trapped, reducing the strength of the finished component part.
During subsequent processing of the finished component part, organic nonwovens have clear advantages due to their better drapability. In tests it was shown that extreme angles and details could be formed. Up to now forming has been tested only on smaller component parts up to a size of 200 mm x 200 mm. The developers anticipate these results will be transferable to larger parts. For more in-depth testing and further development of this technology to make it market-ready, the developers at
Reifenhäuser Reicofil are currently looking for partners in the industry. Together, it is planned to investigate which new lightweight construction markets can be opened by the new semi-finished product and the new manufacturing process.
The new composite fibre material and the new manufacturing process will be presented to the public for the first time at the K 2013, which runs from the 16th to the 23rd of October in Düsseldorf.
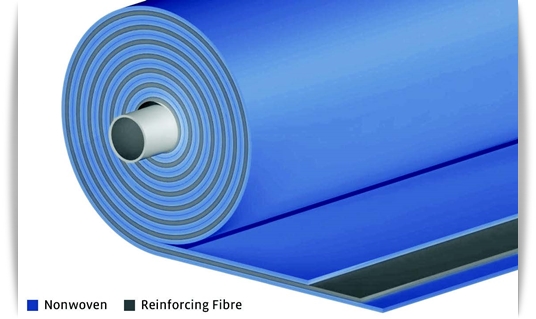
New rollable fibre-reinforced plastic combined with nonwovens
Internet: www.reicofil.com
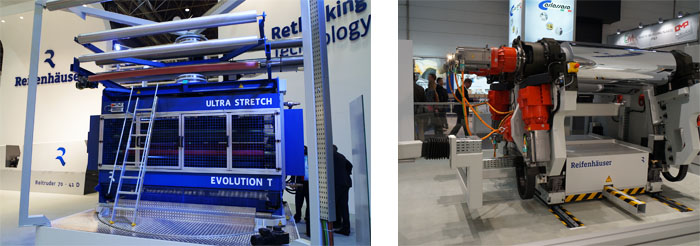
pic:Brilliant Show at K 2013
E-News Categories
Máquina Sopladora
- Máquina automática de moldeo por soplado
- Maquinaria de moldeo por soplado
- Máquinas de moldeo por soplado de extrusión continua
- Máquina de extrusión y soplado
- Extrusora Sopladora De Plastico
- Máquina de moldeo por soplado totalmente eléctrica
- Máquinas de moldeo por soplado hidráulico
- Máquina de moldeo por soplado de plástico
Extrusora de Plástico
- Línea de extrusión de película de burbujas de aire
- Línea de extrusión de película de burbujas de aire
- Línea de coextrusión de hoja de burbujas de aire
- Máquinas para hacer bolsas
- Blow Film Making Machine
- Blow Film Exusion
- Máquina de hacer películas sopladas
- Máquina de película fundida
- Máquina de recubrimiento
- Línea de extrusión de láminas de espuma EPS / EPE
- Extrusora
- Máquinas laminadoras
- Extrusion Lines For Filaments and Yarn
- Extrusion Lines For Pipes and Profiles
- Maquinaria de extrusión de monofilamento
- Línea de extrusión monofilamento
- PET Strapping Band Extrusion Lines
- Máquinas para fabricar bolsas de plástico
- Coextrusión de película plástica
- Máquinas de fabricación de tubos de plástico
- Máquina de fabricación de tubos de plástico
- Manguera de PVC que hace la máquina
- Máquinas para hacer paja
- Extrusora de doble husillo
- Extrusoras de doble husillo
- Máquina de fabricación de bolsas tejidas
Máquina recicladora de Plástico
- Línea de lavado de botellas
- Trituradora
- Granulador
- Pelletizador
- Pelletizadores
- Pelletizing Machines
- Línea de Reciclaje de Botellas PET
- Línea de lavado en caliente de PET
- Peletizadora De Plastico
- Equipo de reciclaje de plástico para preprocesamiento
- Máquinas de reciclaje de plástico
- Máquina de reciclaje de residuos plásticos
- Reciclaje de líneas
- Reciclaje de la máquina
- Desfibradora De Plastico
- Exprimidores
- Linea de lavado de plastico
- Equipo de Reciclaje de Residuos